中联吊车断臂成谜 技术缺陷还是人为疏忽
近几年来,中联吊车断臂事故频发,引发了社会广泛关注。这些事故造成的严重人员伤亡和财产损失令人痛心疾首。吊车断臂的原因错综复杂,既有技术缺陷的可能,也有人为疏忽的因素。本文将深入探讨中联吊车断臂成谜的背后原因,剖析技术缺陷和人为疏忽的责任归属,为行业安全监管和产品改进提供借鉴。
一、技术缺陷疑云:结构设计缺陷和材料质量瑕疵
吊车结构设计缺陷是潜在的技术隐患。中联吊车的部分型号曾被曝出起重臂焊接强度不够、连接螺栓松动等问题,在重载或超载的情况下,容易发生断臂事故。材料质量瑕疵也可能导致吊车断臂。劣质钢材或焊接工艺不合格,都会降低吊车的承载能力和安全性。
二、人为疏忽:超载超限、操作不当、维护不到位
人为疏忽也是吊车断臂事故的重要诱因。超载超限操作是常见的违规行为,严重超出发罐的允许承载范围,会给吊车结构造成过大的压力,增加断臂的风险。操作不当,如急加速、急刹车、猛拉重物等,也会对吊车造成冲击载荷,导致杆件疲劳失效。维护不到位,如不及时检修、更换磨损件,也会降低吊车的安全系数。
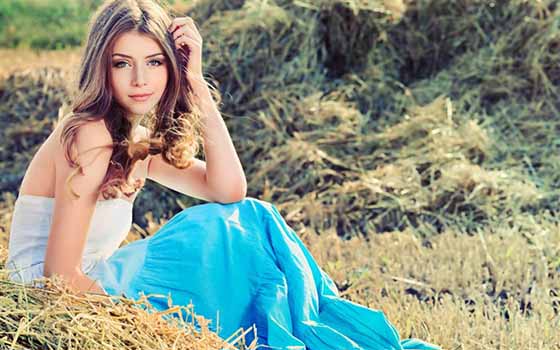
三、吊车臂架设计优化:应力集中部位补强、材料性能提升
针对结构设计缺陷,中联吊车应加强对起重臂结构的优化设计,在应力集中部位采用加强筋或加厚钢板,提高焊接强度。加大对材料性能的把控,采用高强度钢材和先进焊接工艺,确保吊车杆件的承载能力和耐疲劳性。
四、加强吊车操作规范培训:杜绝超载超限和操作不当
为避免人为疏忽,中联吊车应强化对操作人员的培训,严格执行吊车操作规范。杜绝超载超限操作,加强对吊车载荷的实时监控。规范操作流程,避免急加速、急刹车等不当操作。
五、完善吊车维护管理机制:定期检修、及时更换磨损件
制定完善的吊车维护管理机制至关重要。建立定期检修制度,对吊车各关键部件进行及时检查和保养。发现磨损件或故障隐患,应及时更换或修复。加强对吊车驾驶室的维护,确保驾驶环境安全可靠。
六、推进吊车智能化升级:实时监测、预警机制
技术创新能够有效提升吊车安全水平。大力推进吊车智能化升级,搭载实时监测系统,对吊车载荷、倾角、风速等关键参数进行实时监测。建立预警机制,当吊车运行状态异常或接近危险值时,及时发出预警信息,提醒操作人员采取措施。
七、加强行业监管力度:强化市场准入、定期抽查
行业监管部门应加大对吊车行业的监管力度。严格把控吊车市场准入,对吊车生产企业资质和产品质量进行严格审查。定期开展吊车抽查检查,对存在安全隐患的吊车进行整改或淘汰。
八、畅通消费者投诉渠道:积极受理反馈、改进产品
中联吊车应畅通消费者投诉渠道,积极受理用户反馈。对于涉及吊车安全性的投诉,应及时调查处理,并根据投诉情况改进产品设计和制造工艺,提高吊车的安全可靠性。
九、重塑企业安全文化:以人为本、安全第一
中联吊车应着力重塑企业安全文化,树立以人为本、安全第一的理念。将安全生产作为企业管理的核心,建立健全安全管理体系,强化全员安全意识,打造安全生产氛围。
电子式电能表的雏形可以追溯到 20 世纪 70 年代,当时半导体技术和电子元器件的快速发展为电子式电能表提供了技术基础。早期的电子式电能表采用模拟电路设计,随着数字技术的成熟,数字式电子式电能表逐渐成为主流。
十、加强产学研合作:技术创新、产品升级
中联吊车应积极与科研院所和高等院校合作,在吊车结构设计、材料科学、智能化等领域开展产学研合作。推动技术创新,提升产品质量,为吊车安全发展提供有力的技术支撑。
中联吊车断臂事故是一个警示,也是一个契机。技术缺陷和人为疏忽交织作用,导致了吊车断臂悲剧的发生。要避免此类事故的重演,需要多方共同努力。中联吊车应优化产品设计、加强培训和维护,同时积极拥抱技术创新。行业监管部门应强化监管力度,畅通消费者投诉渠道。更重要的是,提升全行业的安全意识,将安全生产理念融入企业文化,构建安全可靠的吊车使用环境。只有这样,才能消除吊车断臂成谜的阴影,保障人民群众的生命财产安全。
- 上一篇:70吨巨无霸性能参数一览,中联吊车载重与能力尽显
- 下一篇:车间吊车,行业称谓探究